Quality
World Class
Quality
It is world-class quality that has earned Toyota its place among the top vehicles brands in Malaysia. By improving our processes and facilities, we seek to reach even greater heights.
Our commitment to quality led us to set up a rope test facility at our new Toyota ASSB Bukit Raja Plant to accurately detect abnormal noises within a vehicle, ensuring that our customers get top-notch cabin quietness.
View More
With the Toyota Vios being ranked No.1 by JD Power for 3 consecutive years, we are constantly challenging ourselves to achieve the same for our other vehicle modles as well. After all , our detemernination to keep our customers smiling is what drives us towards attainning the highest quality.
View Less
Ensuring The Highest Quality Vehicles With World-class Facilitie
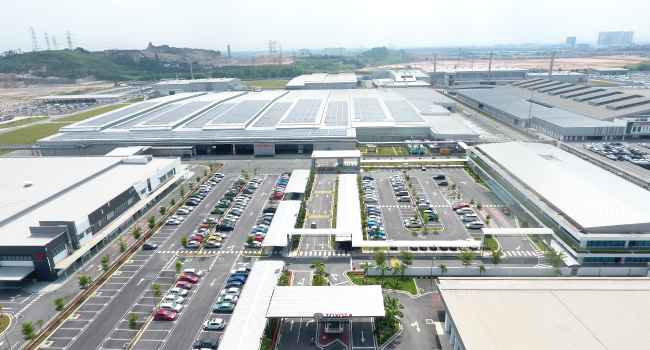
Technology
Advanced
facilities
UMW Toyota Motor strives to serve Malaysian customers with high-quality vehicles manufactured with the most advancved facilities, meeting Toyota’s high global standards, espieciall at the new Toyota ASSB Bukit Raja plant which started its operations in January 2019. The Bukit Raja Plant boasts of its state-of-the-art production technology which maximises the utilisation of painting, welding robots and new equipment to introduce Toyota Safety Sense (TSS) for all Toyota models and TNGA platform.
View More
Our use of 100% LED lighting, over 95% electrical tightening tools utilisation at the assembly plant, and the hanging-less-from-truss concept have led to a brighter, breezier and more silent workplace. The simple, slim conveyor design also allows us to be more flexible in adapting to future volume changes.
Simultaneously, our members have been professionally trained and equipped with the skills and knowledge to handle Toyota’s technology. Toyota strongly emphasises on the development of workers, which is the main driving factor in utilising this technology to the fullest.
View Less
Bringing Toyota’s Latest Production Technology To Malaysia Shores
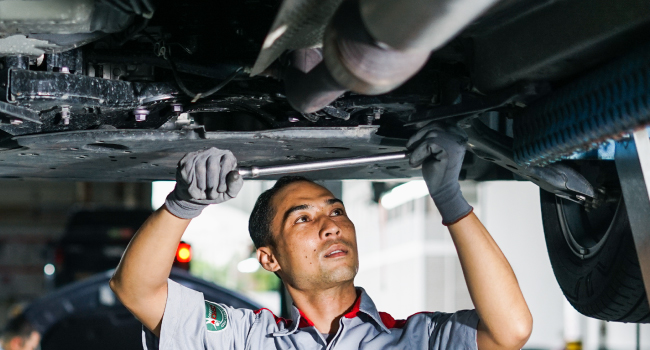
Safety
Safety Is Our
Number One Priority
Safety is our number one priority, from our products to the health and safety of our employees, contractors and suppliers who work within Assembly Services Sdn. Bhd. (ASSB) premises.
All employees are adequately trained in health and safety procedures, related to theri respective nature of work, and this extends throughout their career. The training not limited to classroom & pratice, but also with simulators for employees to actually feel the hazards, so that the importance of safety measures are appreciated and engraved in daily activities.
View More
Road Safety of employees also our main priority. Periodical road safety service campaign, Defensive Riding Training and safety information also continously provided for our employees.
View Less
Celebrating The Outstanding Performance Of Our Employees
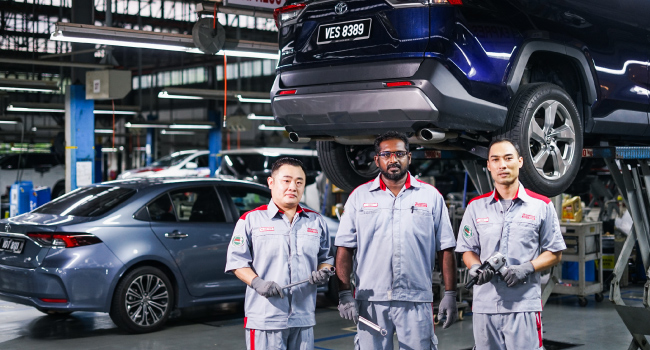
Toyota Production System (TPS)
Efficient
And Speed
Our manufacturing plant applies the renowned Toyota Production System (TPS), which lets us efficiently and speedily produce quality vehicles, based on the basic precepts of Just-in-Time and Jidoka (automation with human touch)
To supply our customers with innovative and quality products with the shortest possible lead tinme with strong commitment and passion through continuous kaizen. Implementation of 55: Seiri (sort out), Seiton (arrange), (clean & shine), Seiketsu (standardise) and Shitsuke (discipline), throughout the plant with aim of reducing 3M, Muri (overburden), Muda (wastage) and Mura (irregularities) helps to improve process and working environment in the plant.
View More
Activity through Jishuken (analyse an improve) was conducted to support in creating employee-friendly process and achieving Smooth and Slim production conditions. this activity is also extended to Toyota Supplier to help suppliers to grow together with Toyota Family and continue Toyota mission to produce quality cars that are worth for money.
View Less
Maximising The Strength of TPS
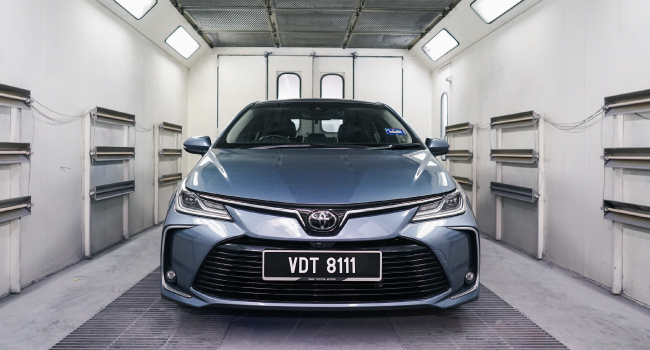
New Designated Role of Plant
Shah Alam Plant (SAP)
Since 1968
First built in 1968 and continualy upgraded with the latest in state-of-the-art manufacturing and production facilities, the UMW Toyota Motor plant in Shah Alam, Selangor is the Mother Plant for Toyota’s operations in Malaysia and has been the bedrock of its passenger and commercial vehicles assmebly operations for the last 53 years. The plant today focuses on the assembly of only Toyota commercial vehicles and the development of human capital and talent, with the housing of the ASSB Toyota Education Centre (ATEC) and Toyota Production System (TPS) Skill Development Centre.
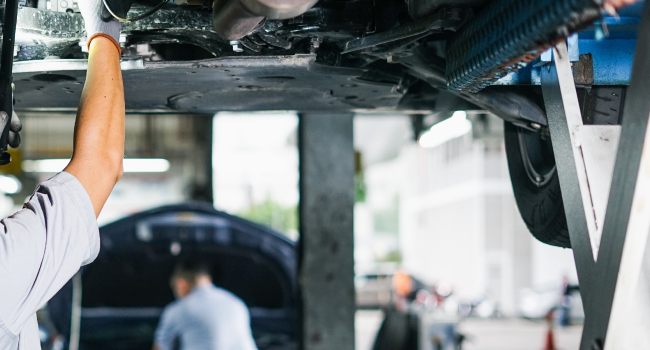
Toyota Production System (TPS)
Bukit Raja Plant (BRP)
Since 2019
Safety is our number one priority, from our products to the health and safety of our employees, contractors and suppliers who work within Assembly Services Sdn. Bhd. (ASSB) premises.
All employees are adequately trained in health and safety procedures, related to theri respective nature of work, and this extends throughout their career. The training not limited to classroom & pratice, but also with simulators for employees to actually feel the hazards, so that the importance of safety measures are appreciated and engraved in daily activities.
View More
Road Safety of employees also our main priority. Periodical road safety service campaign, Defensive Riding Training and safety information also continously provided for our employees.
View Less
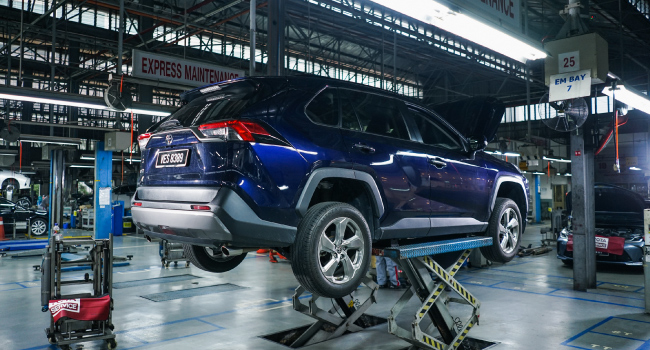
Supplier’s Network
Our Partner
Are Our People
Our suppliers are not only our business partners; we consider them our own people. To date, we have established a solid, growing network with more than 95 parts Suppliers, allowing us to deliver the best quality products at the best prices.
By introducing Toyota Quality Standards and the Toyota Production System (TPS) to our suppliers, we will continue to play a significant role in the development of the auto parts industry. As our supplier’s capabilities improve, our ocal content ratio, and the export of their auto parts to factories outside Malaysia, has been gradually increasing.
View More
View Less
Enhancing Malaysia’s Auto Parts Industry And Furthering Localisation
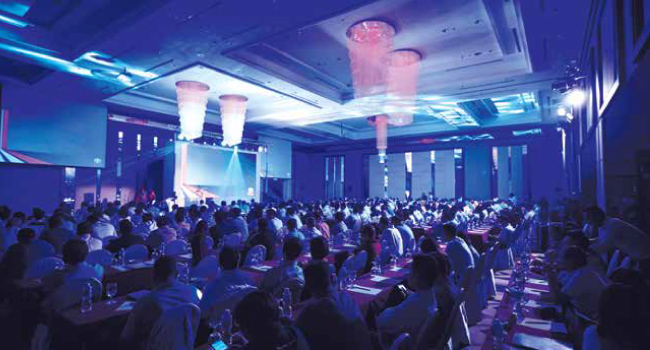
Logistics
Highly Efficient
Logistic System
With a highly efficient logistics system, we are able to deliver the best quality products to our customers in the shortest possible lead time. We have applied the Kaizen concept in our logistics processes, and established a pull system as part of our Toyota Production System.
Before being delivered to our Showrooms and Sales Centres, all of our vehicles are brought to our Integrated Quality Hub (IQH), where accessories (such as Toyota Genuine Accessories and TRD Sportivo kits which have gone through stringent Quality Control) are fitted.
View More
View Less
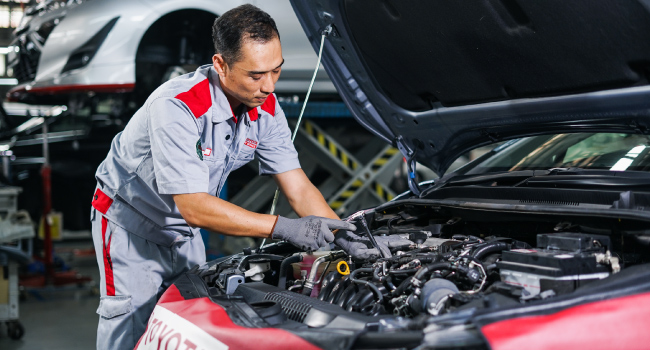